Titanium has developed remarkable qualities over the years, with its development and research bringing out impressive specifications.
Titanium has several advantageous characteristics which makes it the most preferred material for construction, medical and military applications. Characteristics of titanium include:
- Strength
Titanium boasts of an incredible tensile strength of 434 MPa which is three times more than aluminum and two times more than ordinary steel. Titanium also has a low thermal conductivity and does not become brittle even in low temperatures.
- Weight
Despite the strength, titanium is light with a weight of 60% less than that of stainless steel. This has made it suitable for aeronautical applications since it reduces weight load when in motion. Its excellent elasticity and low magnetic permeability makes it perfect for electronic devices.
- Corrosion resistant
Titanium does not corrode easily giving it a longer lifespan than most metals. This ultimately lessens the cost of material replacement, therefore making the use of titanium economical to the user. Titanium is not affected by salty water or by mineral at room temperature.
- Environmentally friendly
Titanium is not hazardous to the environment as its metal ions do not dissolve, therefore reducing the risk of metal allergies.
Types of titanium
Titanium has different grades and varieties of alloys which vary in chemical elements and in strength, malleability and flexibility. Titanium is created and formulated in different ways each with a distinctive attribute. These attributes categorize the product into either:
- Alpha structure
- Beta structure
- Alpha-beta structure
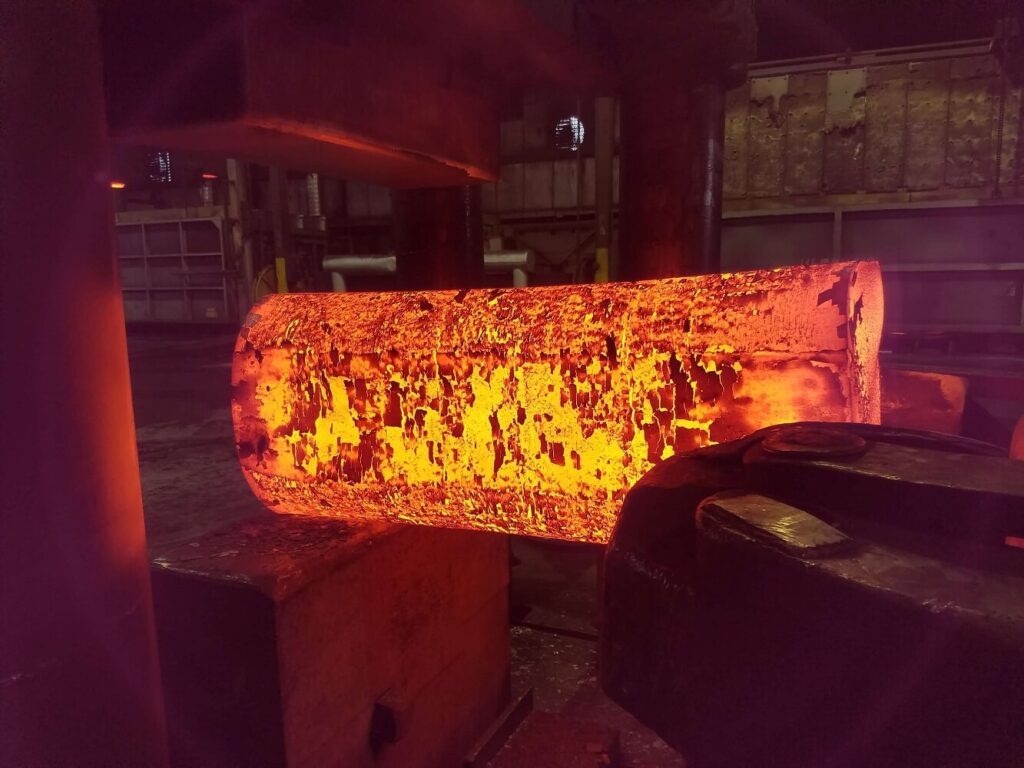
Titanium grade 1 is the softest and suitable for chemical processing applications. Grade 2 is widely available and the most common in the market, since it is easily welded. Titanium grade 4 is the strongest and best used for aircraft parts, hydraulic tubing and surgical purposes among others, due to its good formability.
Titanium alloys, with the most common being grade 5, are extremely versatile as they are mixed with aluminum, iron, oxygen, tin and vanadium. The grade 5 titanium alloy is the most widely available as it is recognized for diverse uses. The type of mechanical properties in the different titanium alloys is dependent on the heat treatment condition administered to them. The composition of the materials also helps evaluate the points of stability of the alloy.
Titanium alloys have more malleability, flexibility and versatility than pure commercial titanium since they take on the properties of the material they are mixed with. Titanium alloys are also adjustable and their characteristics can be altered to suit the purpose they are meant for.
Their low density offer the best results when engineered, and produces premium products. Titanium can be welded into different forms and shapes, which depend on the functionality of the end product:
Titanium sheets
These come in various sizes and thickness. Titanium sheets are formed by casting titanium into a thin film, with the help of vapor deposition and evaporation processes. Titanium sheets are flexible and can be bent to accommodate usage in different projects. These sheets are commonly used in aeronautical and marine purposes.
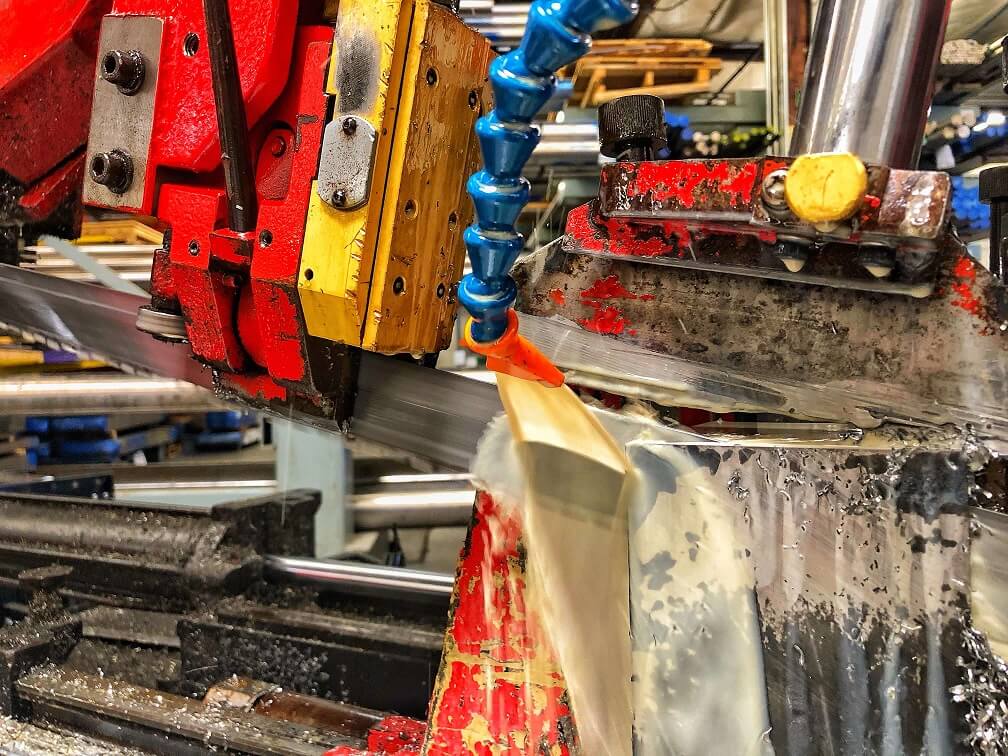
Titanium bars
These are specially formulated in a bar shape to ease on transportation and storage purposes. These bars, which are formed through a process of welding and hot rolling, come in different grades and diameter specifications. Due to their lightweight and strength, titanium bars are used in architecture, technology and industrial usage.
Titanium plates
These come in different thickness structures. Titanium plates are particularly used due to their thinness, as they can’t be bent or shaped any other way. They are used in industrial, armor and technological purposes as well. Medical research also classifies the use of titanium plates in orthopedic and biomedical purposes, as titanium plates are not affected by rays.
Market trends
The Titanium Sheet market is rapidly changing with the emerging trends and opportunities in the industry. According to the Global Titanium Sheet market industry report, the market growth is set to grow exponentially by 2025. This analysis report factors in the different market segments and the influence of the market players in the industry.
Companies manufacturing and producing titanium are embracing innovative product development in order to meet the demanding market. Recent market trends predict a possible change in alloy structure. For instance, the titanium alloy structure synthesized to different alpha or near alpha components.
These alloy structures contain alpha components aluminum, tin and oxygen and remain in the alpha phase at room temperature. They can also be used in higher temperatures than alpha-beta alloys, making them candidates for aeronautical use in automotive production given the recent surge in airplane manufacture.
Despite the titanium market being dominated by major key players, companies with the right strategy can permeate the market, by understanding the economic shifts and keeping up with the technological advancements.